Why do I need a BIM Execution Plan for effective collaboration?
When it comes to construction projects, design professionals and contractors often cite this old axiom —
There are three components in performing successful construction projects: Cost, Time, and Quality.
In many cases, clients can only pick two to control and the designers and contractors will control the remaining if the client cannot be responsible for all three.
Projects employing Building Information Modeling (BIM) have the opportunity to have all three components equalized for the successful completion of the project. A careful, well-constructed BIM Execution Plan (BIMExP) developed prior to delving too deeply into the design of the project is a complete necessity.
A properly executed BIM Execution Plan can — and will — result in an efficiently designed, constructed and managed outcome. The importance of all stakeholders in the project (design team, builder, owner and operator) is crucial to the success of the project.
To understand why and how a BIM Execution Plan provides for more effective collaboration, it helps to understand the evolution that brought us to BIM.
Prior to the advent of computer aided design (CADD) and BIM, drawings were produced by hand. It was often the role of the architectural project manager or project architect to produce a "cartoon set" of the drawings that would be produced for the Construction Documents. The cartoon set provided a road map for the production of the documents. Depending on the architect’s fee, the Construction Documents would be organized to provide the necessary information to gain a building permit and construct the projects. In many cases the hand-drawn system led to increased project costs for lack of collaboration of the builder and the owner.
For more on BIM Execution Plans, join Greg Burke at the AIA Florida 2021 Convention for his presentation BIM Execution Plan: How Do I Prepare One?
In the 1960's the construction industry saw the advent of the Construction Manager. A unique group of individuals who primarily held MBA degrees who were now entrusted with the management of the design and construction process of a project. In later days, universities developed construction management degrees that would couple the business administration need with the construction capabilities necessary to deliver a better construction process.
In the large projects the client and operator were usually an integral part of the team. But in many smaller projects, general contractors hung out their shingle as construction managers with no real expanded training or qualification than they had as general contractors. The latter system again often led to projects with cost overruns and not the greatest of collaboration efforts.
CADD held the promise for better coordination and collaboration than the hand drawn system. Drawing files were exchanged in a manner not demonstrably different from how they were exchanged in the hand system. It should be noted that the pin-bar system of creating drawings was an intermediate step between hand-drawn and computer generated drawings.
Pin bar was a system of overlaying several layers of information on mylar sheets to complete a single drawing, It was the precursor and intelligence that led to the layer system used by many CADD programs. It really did very little to increase the collaborative efforts of the construction process. CADD in itself did make some aspects of the design process a bit more efficient. Changes to documents were more efficiently made, transferring information became easier between all parties, but the collaboration remained about as efficient as the hand drawn system.
Effective collaboration, as always, depended on the capability of the team leader.
Adding up Efficiency
- The efficiencies of BIM have been shown to be in the range of 25-30% (1). The efficiency is an outgrowth of better managed and planned projects.
- Construction costs have also shown a reduction in the realm of 22% (2).
While there is currently a low level of digitalization in the construction industry, the gains noted above are made possible by developing a well-planned, effectively-communicated and coordinated BIM Execution Plan.
Interoperability of software systems are often cited as the main impediment to efficient workflows of information. However, both Revit and ArchiCad have developed software that can effectively solve the issues when all of the team members are using software created by their respective companies.
Where the software is used and produced by more than one company, the system of using Industry Foundation Class data assignment to the elements of the BIM model become an effective way of collaboration between all of the project team.
The Industry Foundation Class (IFC) system of classifying elements of a building information model was created providing a platform neutral specification format controlled by single vendor or vendors (3). IFC allows for the free flow of information between all of the project team members. IFC is registered with an International Standard ISO 16739-1:2018.
The BIM Development Timeline
The advent of BIM dates back to the 1970's.
Several small companies developed programs that were extremely expensive to operate as computers had not reach the maturity that we see today. The actual involvement by software producers to insert themselves into the construction process did not begin until the early 21st century. A few companies had been producing their software for several years in the late 20th century:
- Graphisoft began producing
ArchiCad in 1987.
- Not given much credit, Charles River Software began producing
Revit in 1997. (Full disclosure, I was a part of what Charles River called its
Pioneer Program, which consisted of 20 architects from around the country who were using the software to ascertain what worked and did not and what needed to be improved.)
- AutoDesk, the owners and developers of
AutoCADD, purchased the rights from Charles River in 2002 and has developed and marketed it ever since.
- Several other companies have developed BIM software, such as Bently, but without the market share of Revit or ArchiCad.
Why is a BIM Execution Plan (BIMExP) necessary?
Just as the "cartoon set" for hand drawings, the BIMExP provides the road map necessary for the effective execution of the design, construction of the project and its eventual maintenance. It is vitally important that there be a lead consultant, either the architect or construction manager of the project to take the control of establishing the Plan. The responsibility for leading the project team in defining the BIMExP needs to be contractually agreed upon and documented through a standard document such as those provide by the American Institute of Architects or other project specific prepared document.
A properly executed BIM Execution Plan can — and will — result in an efficiently designed, constructed and managed outcome.
With responsibility for the lead on creating the BIMExP established, the lead must involve all of the stakeholders who will play an import part in designing, owning and operation the building or buildings.
For instance, if the final model will be used for maintenance and inventory of assets for the building, the facilities department is and should be a member of the team that will prepare the BIMExP.
The Kick-Off Meeting
With all of the team members assembled an initial kick-off meeting is necessary for the leader to determine what the final outcome of the model will be. This necessitates a bottom up type of planning in that assumes the final results (operations) and works backwards to the conceptual design of the project. During the kick-off meeting roles and responsibilities are established. It is likely that Programming and other Pre-design services have been performed in order to establish goals and objectives for the project.
The kick-off meeting will identify what consultants are using what software, versions, etc to produce documents. Where everyone is on the same page with software platforms from the same companies, a no-brainer scenario can be established. Where consultants, constructor and owner use the same platforms one of several ways to work in real time are available.
For instance, if the lead consultant chooses Revit, AutoDesk BIM 360 allows for the real-time collaboration. If ArchiCad is chosen, Graphisoft’s BIM Server provides the same real time collaboration. Where different platforms are used, the effective communication and collaboration can only be accomplished through the use of the IFC system. The identification of these constraints are necessary to be established at the kick-off meeting.
The IFC system will accurately identify construction elements, serial numbers, installation data, warranty data and other information that will be required by the entire project team. If the model will be used for facilities maintenance, information relative to warranty, cleaning, maintenance and other issues can be identified in the model for the facilities effective management of the inventory. Items such as this show the necessity for full coordination and collaboration of the entire team.
Kick-off meetings will establish the level of development (LOD) required for the model at the various stages. It is normal for many projects where the final model (termed the federated model) is delivered by the design team at a level of development of 2 (LOD 200).
The federated model by implication is a model with all construction elements included. LOD200 may in effect have several different levels of documentation. The architect is usually developing their portion of the model at LOD300 or 350 which would equate to a highly developed Construction Document level of CADD drawings, while the MEP consultant maybe at LOD200, a more schematic level. This type of model would likely have a contractual agreement for the construction of the building and no owner occupancy facilities maintenance required.
MEP Construction Documents delivered to building departments as 2D drawings are often identified as schematic in nature and will rely on the constructor to provide the necessary coordination of the systems into the construction of the building. This seems to negate the entire need for a BIM system of delivery. If we are using BIM to provide schematic type design, we are using sophisticated drafting tool rather than a collaborative information modeling tool.
Additional meetings may be as numerous as necessary for the team to
produce an effective BIMExP. Internal meetings for each individual consultant are necessary to determine how much and what will be documented. Subsequent meetings with the entire project team are then organized to refine and hone of the information that will be delivered. Where a project’s model will be federated and used in facilities management a LOD500 is necessary. It should be noted that here may be several meetings held prior to beginning and real model development. Schematic design maybe begin, but data should be beginning to be incorporated into the model in a general manner.
Without an effective BIMExP, the collaboration effort for the project can fall apart, leaving the owner holding the bag.
What can happen when a BIMExP is not effectively planned?
To answer this question, I'll refer to a specific case I was involved in a few year ago. I was brought into a lawsuit as an expert witness for a project that was executed from 2015-2017. The project was for a five-story assisted living facility and two associated outbuildings. The building was to be designed and constructed using building information modeling for the design and construction of the buildings.
Architects were selected and contracts executed. The design architect was a large, well-respected out-of-state firm known for designing the type of facility. The design firm associated with a local firm for administration and BIM support. A nationally-known construction management (CM) firm was retained for the construction of the project. Both firms were responsible for creating models of their designs and construction.
While the construction manager held all of their consultants to creating BIM LOD400 models, only the structural and MEP sub-contractors actually took on the responsibility. The construction manager’s sub-contract form included a rider that stated the construction manager would create and monitor a BIMExP and the sub-contractors would be required to create their models, not relying on the models created by the design team.
During the design phase, the mechanical contractor was hired by the construction manager with a design assist agreement that did not adequately identify roles and responsibilities for all parties. This in itself created some of the issues that would lead to the lawsuit. The construction manager used no less than three individuals to direct the BIMExP. It became clear early on that neither the construction manager nor the sub-contractor had a full grip of the responsibilities required for the effective execution of the construction.
At no time was there adequate communication to the roles and responsibilities of the entire project team in delivering the facilities. Nor were there any contractual arrangements identifying who was to lead the BIM effort on the project. In the end the project was nearly six months behind schedule with several cost overruns.
Design team models were analyzed for conflict prior to the sub-contractor signing its agreement with the CM. Design team models identified a large number of conflicts. In information gleaned from depositions of the design team members, it was clear that some of the team members (both design and construction) were under-qualified in their knowledge of the deliverables necessary to the contract. This led to the sub-contractor and CM having many issues during the construction of the building. The sub-contractor did not enough employ qualified staff to execute their models and subsequent shop drawings leading to several tear-outs and re-constructs on the project.
In the end, there was no federated model of the project which was required of the sub-contractors and there was no effective use of BIM on the project. The mechanical contractor initiated suit against the CM for lack of supervision of their BIMExP. Both parties agreed to a settlement and, in the end, as is the case with many suits, the lawyers were the winners.
The above example provides information as to why it is critically important to prepare, execute, and monitor a BIM Execution Plan.
It is necessary that the lead have a thorough understanding of not only the level of development necessary, but a complete understanding of the contractual requirements of the entire project team. Without an effective BIMExP, the collaboration effort for the project can – and will – fall apart leaving the owner holding the bag.
Greg Burke, FAIA
Reference
1 Marketsandmarkets.com, Building Information Modeling Market. June 2020
2 ibid
3 Wikipedia, Industry Foundation Classes
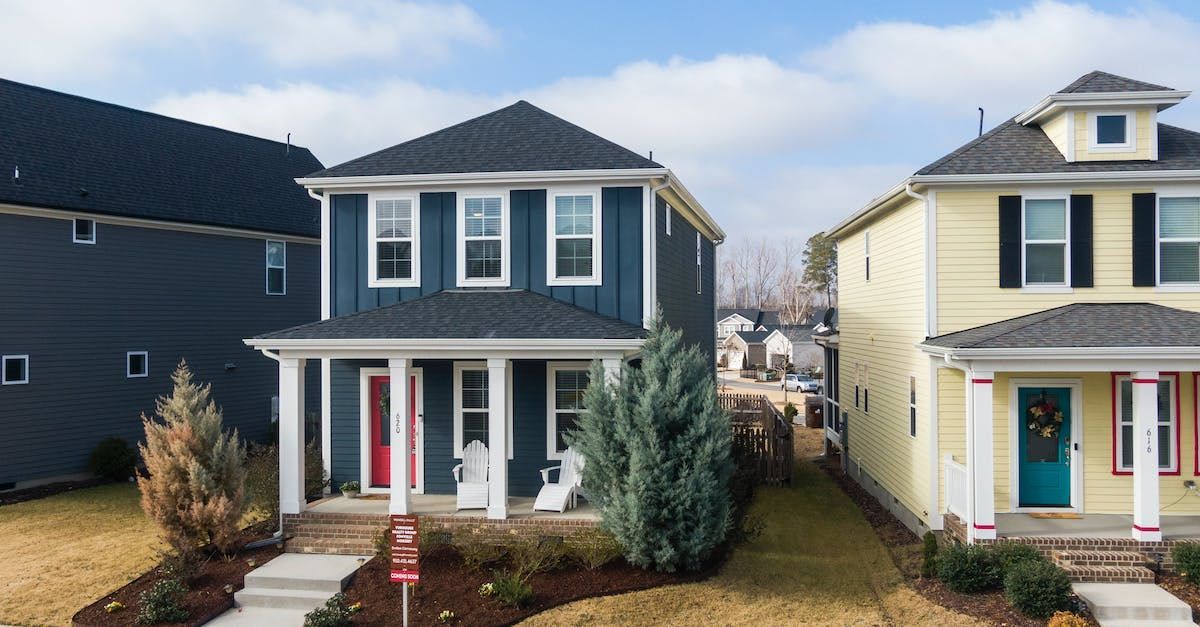